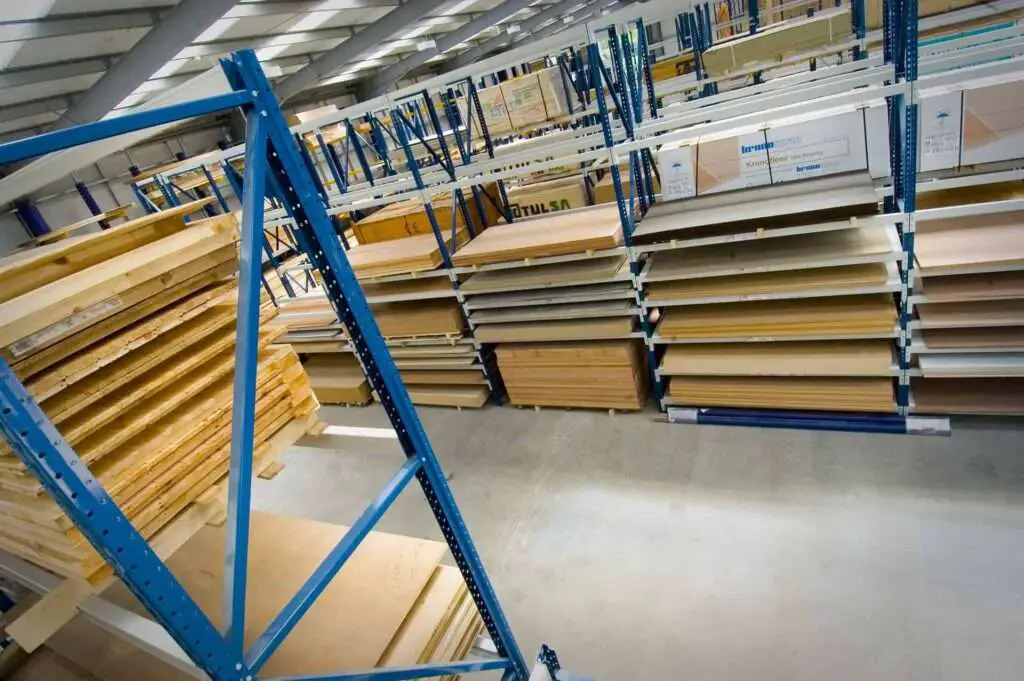
A marine-grade plywood is made from a higher-quality of wood and glue specially treated to withstand exposure to water, making it ideal for boat building, dock building and other outdoor projects.
What is marine-grade plywood?
Marine-grade plywood, also known as marine plywood, is a type of plywood that is specifically designed for use in harsh marine environments.
Unlike regular plywood, marine-grade plywood is made with a higher quality of wood and glue that makes it highly resistant to water, humidity, and rotting.
This type of plywood is ideal for boats, docks, piers, and other marine structures that are constantly exposed to water and moisture.
Different Types of Marine-Grade Plywood
Here are the most common types of marine-grade plywood and their characteristics:
1. Okoume Plywood:
Okoume plywood is one of the most popular types of marine-grade plywood. It is lightweight, strong, and easy to work with. It has a beautiful, uniform grain pattern, and is known for its ability to resist rot, decay, and insects. Okoume plywood is commonly used for boat building, cabinetry, and other marine applications.
2. Meranti Plywood:
Meranti plywood is another popular type of marine-grade plywood. It is also lightweight and strong and has a uniform grain pattern. Meranti plywood is highly resistant to water, rot, and insects. It is often used for boat building, decking, and other marine applications.
3. Douglas Fir Plywood:
Douglas fir plywood is a strong and durable type of marine-grade plywood. It has a straight, uniform grain pattern, and is resistant to rot, decay, and insects. Douglas fir plywood is commonly used for boat building, decking, and other marine applications.
4. Teak Plywood:
Teak plywood is a beautiful and highly sought-after type of marine-grade plywood. It is known for its strength, durability, and resistance to water, rot, and insects. Teak plywood is commonly used for boat building, cabinetry, and other high-end marine applications.
5. Baltic Birch Plywood:
Baltic birch plywood is a strong and durable type of marine-grade plywood. It has a tight, uniform grain pattern, and is resistant to water, rot, and insects. Baltic birch plywood is commonly used for boat building, decking, and other marine applications.
Advantages and disadvantages of marine-grade plywood
Advantages
- High resistance to water damage: Marine-grade plywood is designed to withstand exposure to water. This plywood is made with a special adhesive that can handle prolonged exposure to moisture without deteriorating or delaminating.
- Strong and durable: Marine-grade plywood is made from high-quality hardwoods and is generally thicker and stronger than other types of plywood.
- Easy to work with: Despite its strength, marine-grade plywood is easy to cut, shape, and drill.
Disadvantage
- Expensive: One of the main disadvantages of marine-grade plywood is its cost. This type of plywood is generally more expensive than other types of plywood, which can be a significant barrier for budget-conscious builders.
- Limited availability: While marine-grade plywood is available at many hardware stores and lumberyards, it’s not as widely available as other types of plywood. This can make it difficult to find the right size and thickness for your project.
- Can still rot: While marine-grade plywood is resistant to water damage, it’s not completely impervious. Over time, it can still be susceptible to rot and decay if it’s not properly sealed and maintained.
Also Read:
Boatbuilding Materials: A Comprehensive Guide
All About Fiberglass: A Boat Builder’s Material Guide
What is the best grade of marine plywood?
The highest grade is AA. AA grade signifies that the plywood has no defects and has been treated with a waterproof adhesive.
While AA-grade plywood may be the best option for critical applications, such as boat-building or marine construction, it is also the most expensive.
For most marine projects, however, A-grade plywood is sufficient. A-grade plywood also has no visible defects, and it is also treated with a waterproof adhesive.
While it may not be as perfect as AA-grade plywood, it is more affordable and suitable for most marine projects.
Lower grades, such as B and C, may be used for non-critical applications, but they may have visible defects that affect their strength and durability.
Is marine grade plywood waterproof?
It is true that marine-grade plywood is more water-resistant than regular plywood, but it is not completely waterproof.
Marine-grade plywood is constructed using a specialized glue that is more water-resistant than the glue used in regular plywood.
Additionally, marine-grade plywood is typically made from hardwoods that are naturally more resistant to water damage, such as teak or mahogany.
However, if marine-grade plywood is continuously exposed to water, it will eventually begin to absorb it and break down. To avoid this, it is important to properly seal and maintain marine-grade plywood to keep it water-resistant.
How do you waterproof marine plywood?
There are several ways to waterproof marine-grade plywood, Here are some options to consider:
1. Sealers: Sealers are the easiest way to waterproof marine-grade plywood. They work by penetrating the wood fibers and filling any gaps or pores in the surface. Sealers are available in various formulations, including oil-based, water-based, and solvent-based.
2. Paint: Paint is another way to waterproof marine-grade plywood. It creates a barrier between the wood and the moisture in the air. Paints are available in various colors and finishes, and they offer long-lasting protection against water damage.
3. Varnish: Varnish is a clear protective coating that is applied to the surface of marine-grade plywood. It provides excellent protection against moisture and UV rays.
4. Epoxy: Epoxy is a two-part system that consists of a resin and a hardener. When combined, they form a waterproof and durable coating. Epoxy is an excellent choice for marine-grade plywood that will be exposed to harsh environments, such as boats and docks.
Marine grade plywood vs treated plywood
Marine-grade plywood is designed explicitly for use in humid and wet environments, such as boat building, dock construction, and other marine structures.
It is typically made from hardwood species such as teak, mahogany, and Okoume. This type of plywood has a higher degree of water resistance, is stronger, and has fewer voids or defects in the core layers, making it more durable than regular plywood.
Treated plywood, on the other hand, is made by injecting wood preservatives into regular plywood to prevent rot, decay, and insect infestation.
This type of plywood is commonly used for outdoor construction projects that are exposed to weather and moisture, such as sheds, decks, and fences.
Treated plywood is often cheaper than marine-grade plywood but lacks the superior strength, durability, and water resistance of the latter.
Melamine vs Marine plywood
Melamine plywood is made by applying a thin layer of melamine resin to the surface of the plywood. This makes the plywood waterproof and resistant to stains and scratches. However, it is not as durable as marine-grade plywood, and it is more prone to chipping and peeling over time.
On the other hand, marine-grade plywood is made from high-quality wood and is specifically designed to be used in wet or damp environments.
It is treated with special chemicals to make it resistant to rot and decay, and it is typically thicker and more durable than other types of plywood.
What is MDF, ACX, and CDX plywood?
MDF stands for medium-density fiberboard, and it is made from wood fibers and resin compressed together to form a dense, flat panel. It is not typically used in marine applications due to its poor moisture resistance, but it is often used for furniture and cabinetry.
ACX plywood stands for “A-grade, exterior, sanded,” and is a type of plywood that is often used for outdoor projects such as sheds or signs. It has a smooth surface and is typically made from hardwood veneers.
CDX plywood, on the other hand, stands for “C-grade, exterior, and either sanded or unsanded.” It is commonly used for construction projects, such as sheathing and roofing, but it can also be used for furniture if it is sanded smooth.
How can you tell if plywood is marine grade?
Here are some ways to tell if plywood is truly marine grade:
1. Look for the stamp or label: Marine-grade plywood should have a stamp or label indicating that it meets the industry standards for marine applications. This stamp or label may include information about the grade, thickness, and certification.
2. Check the veneers: Marine-grade plywood typically has high-quality veneers without any knots, voids, or splits. The veneers should also be thick and consistent in thickness.
3. Examine the glue: Marine-grade plywood is usually made with waterproof glue, such as phenolic or epoxy. You can check the glue by looking for small voids or gaps in the layers of the plywood.
4. Check for rot and decay resistance: Marine-grade plywood is specifically designed to withstand the harsh marine environment, so it should be rot and decay-resistant. You can test this by checking for any signs of mold, mildew, or decay.
Here is a good videos to compare the differences between Marine and other plywoods
What is the best thickness for marine plywood?
Marine plywood typically comes in a variety of thicknesses, ranging from 1/4 inch to 3/4 inch. However, for more heavy-duty projects such as boatbuilding or dock construction, thicker plywood may be required.
A general rule of thumb is to use a thickness of at least 1/2 inch for structural components, and 3/4 inch for flooring or decking.
How much does waterproof plywood cost?
On average, marine-grade plywood can cost between $50 to $200 per sheet, with higher-end options reaching up to $300 or more.
Is marine grade plywood safe to use indoors?
Yes, marine-grade plywood can be used indoors, but it may not always be the best choice.
Marine-grade plywood is specifically designed for use in marine environments where it will be exposed to water, salt, and other elements. As a result, it is treated with preservatives that make it resistant to rot, fungus, and other forms of degradation. These preservatives are not harmful to humans and do not pose any health risks.
However, marine-grade plywood may not always be the best option for indoor use. It tends to be more expensive than other types of plywood, and it may be overkill for indoor applications where the plywood is not exposed to water or moisture.
In some cases, MDF (medium-density fiberboard) or ACX, or CDX plywood may be more suitable for indoor use. MDF is a composite material made from wood fibers and resin, and it is often used in furniture and cabinetry. ACX and CDX plywood are more affordable options that are commonly used in construction and home improvement projects.
How long will marine grade plywood last outside?
If properly maintained and sealed, marine-grade plywood can last for decades. The lifespan of the plywood can also be extended if it is installed correctly, with adequate spacing between panels to allow for ventilation and drainage.
It is important to note that marine-grade plywood is not completely impervious to moisture and can still deteriorate over time if exposed to water for prolonged periods. Regular inspections and maintenance are crucial to ensure the longevity of the plywood.